CNC Lathed Parts: Revolutionizing Metal Fabrication
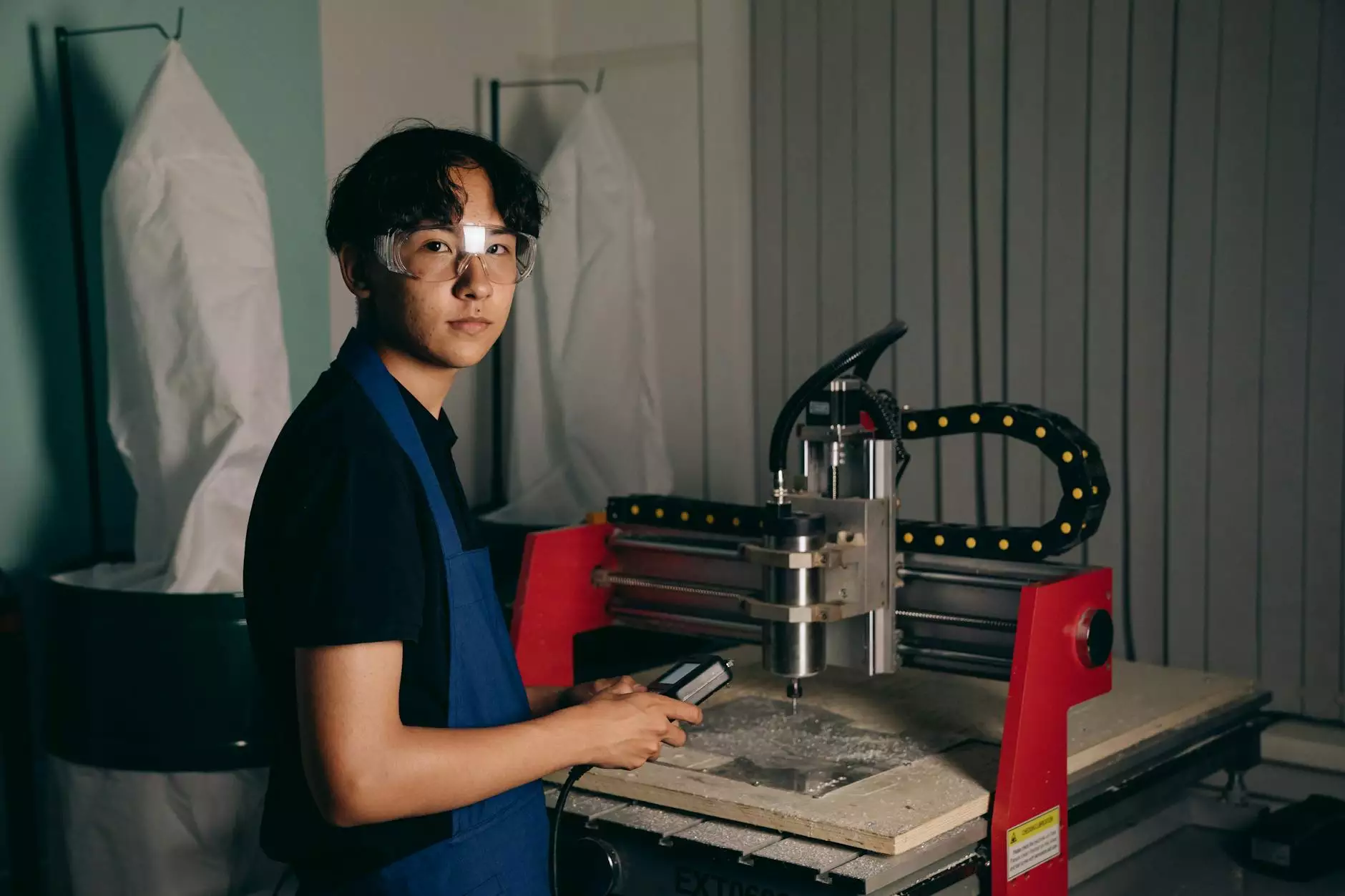
The world of manufacturing is constantly evolving, and one of the most significant advancements in recent years has been the rise of CNC lathed parts. These components have not only streamlined production processes but also enhanced the precision and quality of metal fabrication. In this article, we will delve into the essential features of CNC lathed parts, their applications across various industries, and why they are vital for a business’s success.
What Are CNC Lathed Parts?
CNC stands for Computer Numerical Control, a method used to automate machine tools via computers. CNC lathed parts refer to components created through lathe machining, where materials (typically metals) are rotated against cutting tools. This process allows for the production of highly accurate and uniquely shaped components. The precision involved in CNC machining means that manufacturers can produce complex shapes with a high degree of repeatability and consistency.
The Process of Creating CNC Lathed Parts
The creation of CNC lathed parts involves several key steps:
- Designing: Engineers use CAD (Computer-Aided Design) software to create 3D models of the desired component.
- Programming: The CAD designs are converted into a format that the CNC machine can understand, generating G-code which dictates the machine's movements.
- Machining: The raw material is placed in the CNC lathe, which rotates the material while tools cut into it, shaping it into the specified part.
- Finishing: After the initial machining process, parts may require additional finishing processes such as polishing, coating, or heat treating to achieve the desired characteristics.
Applications of CNC Lathed Parts
CNC lathed parts are incredibly versatile, making them invaluable in various industries:
1. Aerospace Industry
In the aerospace sector, the need for lightweight yet durable parts is paramount. CNC lathed parts are used to create components such as:
- Engine mounts
- Structural components
- Landing gear components
The precision offered by CNC machining ensures that these components meet strict safety standards without sacrificing performance.
2. Automotive Industry
Automotive manufacturers rely on CNC lathed parts for various applications, including:
- Gear components
- Shafts
- Pulleys and crankshafts
These parts contribute to vehicle efficiency, safety, and performance, helping car manufacturers gain a competitive edge.
3. Medical Devices
In the medical field, precision is non-negotiable. CNC lathed parts are used in the production of:
- Surgical instruments
- Implants
- Diagnostic equipment
Because the medical industry places such a high value on accuracy, CNC machining is ideal for creating components that must adhere to strict compliance regulations.
4. Industrial Equipment
Industrial machinery requires robust, reliable parts. CNC lathed parts are integral in manufacturing:
- Hydraulic cylinders
- Pneumatic components
- Valves and fittings
The efficiency of CNC machining meets the demands of heavy-duty applications, ensuring optimal performance over the lifespan of the machinery.
Advantages of Using CNC Lathed Parts
The benefits of integrating CNC lathed parts into manufacturing processes are numerous:
- Precision and Accuracy: CNC machines operate on exact specifications, making them ideal for creating parts that require minute tolerances.
- Efficiency: Once programmed, CNC machines can produce parts quickly and consistently, reducing lead times and increasing productivity.
- Design Flexibility: CNC machining allows for easy modifications to designs without requiring the extensive setup needed for traditional machining methods.
- Reduction of Waste: CNC technology optimizes material use by enabling precise cuts, lowering production costs and minimizing environmental impact.
CNC Lathed Parts and Quality Control
Quality control is a critical factor in manufacturing, especially when it comes to CNC lathed parts. Companies like DeepMould utilize advanced inspection techniques to ensure each part meets stringent quality standards. Measures such as:
- Use of CMM (Coordinate Measuring Machine) for precise measurements
- Regular calibration of CNC machinery
- Implementation of ISO quality management systems
These practices ensure reliability and durability, factors that are essential for customer satisfaction and repeat business.
The Future of CNC Lathed Parts in Metal Fabrication
As technology continues to advance, the future of CNC lathed parts appears brighter than ever. Innovations such as:
- Advanced Materials: Development of new alloys and composite materials expands the possibilities for CNC lathed part applications.
- Automation and Robotics: Increasing automation in CNC machining processes enhances productivity and reduces human error.
- AI and Machine Learning: These technologies will allow CNC machines to optimize production based on real-time feedback and enhance overall efficiency.
Incorporating these advancements positions companies like DeepMould at the forefront of the manufacturing industry, ensuring they remain competitive in a rapidly changing market.
Conclusion
In conclusion, CNC lathed parts are a cornerstone of modern metal fabrication, offering unmatched precision, efficiency, and versatility across various industries. As businesses seek to enhance their manufacturing processes and maintain a competitive edge, the importance of quality CNC lathed components becomes increasingly clear. With ongoing advancements in technology and materials, the future of CNC machining looks promising, paving the way for innovations that will shape the industry for years to come. DeepMould stands ready to fulfill these needs, providing top-quality CNC lathed parts for clients seeking excellence in their manufacturing solutions.